Jet Engine Mechanic
Upon graduation from Basic Training, I was sent to Chanute AFB in
Rantoul, Illinois for technical school. Chanute is about one hour south
of Chicago and just north of Champaign, IL (where the University of
Illinois is). I don't have a lot of memories of this time, but it was
to be the first step in becoming a jet engine mechanic. I was to train
on a Pratt & Whitney powerplant, learning jet engine fundamentals
and how to safety wire (basically wiring two screws so that they can
not loosen).Here are some stories that I happened to remember after all these years:
Fire Drill
One night the fire alarm went off, which is not the funny part. What
was funny was the way some of the girls exited the building, still in
the towels from the shower. Not sure if it was a real fire drill or
someone knowing the girls would just grab a towel and go outside.Parkas
It was October when I got to Chanute AFB and being from Wisconsin, it was still fairly moderate temperatures. However, the people from the southern states were so cold, they would be dressed in there winter issue parkas, me in a t-shirt.Safety Wire
Here is a definition of safety wiring from wikipedia.org:Safety Wire Installation is a fairly simple task, but needs to be
done properly to ensure proper security for the fastener in question.
First, a length of wire is cut off of a spool. The length of the piece
of wire to be used is determined by the distance from the location
where the fastener to be secured is to be attached to another fixed
location, which will act as an anchoring point for the safety wire. The
wire should be cut to be slightly longer than twice that distance. The
next step is to take the removable fastener such as a bolt, drill a
hole through an accessible part of it, fasten it in the desired
location, and then thread one end of the safety wire through the hole
while taking the other end around the outside of the hole in the same
direction as the end that is going through the hole. The wire is then
pulled taut. Using Safety Wire Pliers or the twisting tool of choice,
the wire is then twisted at the optimal number of twists per inch. The
wire is then released from the tool, and the two loose ends should be
adjacent to each other at this stage. One of those ends is then
threaded through some anchor point on the object to which the fastener
being secured is attached. The other end of the wire is then threaded
around the anchor point, and on the opposite side of the anchor point
the twisting process is repeated. When finished, the loose end is cut
off with a pair of diagonal cutters or wire cutters (many Safety Wire
Pliers have a wire cutting feature), such that enough twists are left
to prevent the wire from unravelling. The remaining end can have a
sharp edge from being cut, so technicians will often bend it down
against another hard surface to prevent it from damaging other
components, such as electrical wiring insulation, or from causing
injury to future technicians working in the area.
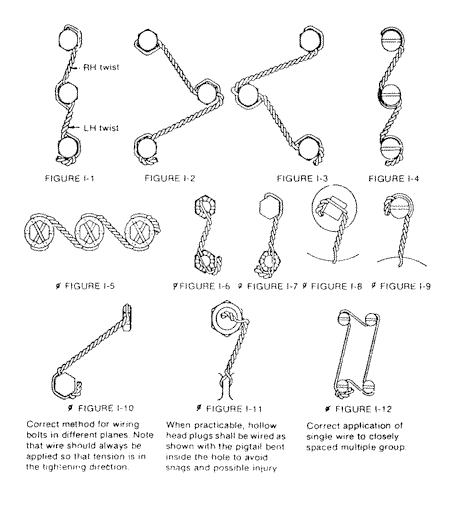